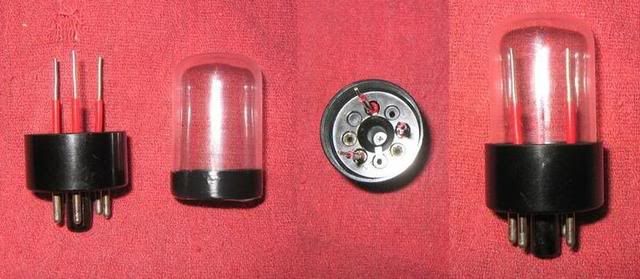
ecir38 wrote:Thought ya'll would get a kick out of this. Here is a SS rectifier that I am preparing for my 300B G*S*G. Just need to solder some UF4007's across the leads now. If anyone is interesting in trying to make one I can give details on how I did this.
EWBrown wrote:
The simple / easy approach for a PAS is to take two UF4007s, connect the two cathodes together, and keep one of the cathode leadslong, then simply plug them directly into the tube socket, (the diode leads are about the same size / diameter as the 12X4 pins) with wo anodes where the plates connect, and the conjouned cathodes to the original cathode / B+ output connection. THis way, it's easily "reversible", and since it is hidden away under the top cover, appearance isn't a real factor.
/ed B in NH
EWBrown wrote:There is another approach, though I've not tested it, connect a 10 ohm 5W WW resistor in series between each "hot" lead of the power trannie's HV secondary and its associated diode rectifier, and then connect one 0.001 uF, 1600V (or greater) disk ceramic cap across the secondary, and a second similar cap between the two diodes' anodes. This results in what is known as a rapid reverse spike recovery filter (RRFSR) , and should work.
The simple version of this is to connect the 0.001 uF 1600V disk ceramic caps across each rectifier diode. Not as effective, it is "old school" approach.
/ed B in NH
ecir38 wrote:
Wondering also for those that have bought a Weber copper cap if they have taken one apart to see how he has them wired. http://www.webervst.com/ccap.html
Users browsing this forum: No registered users and 51 guests